Reducing Cycle Time for Machine Tending with Industrial Robots
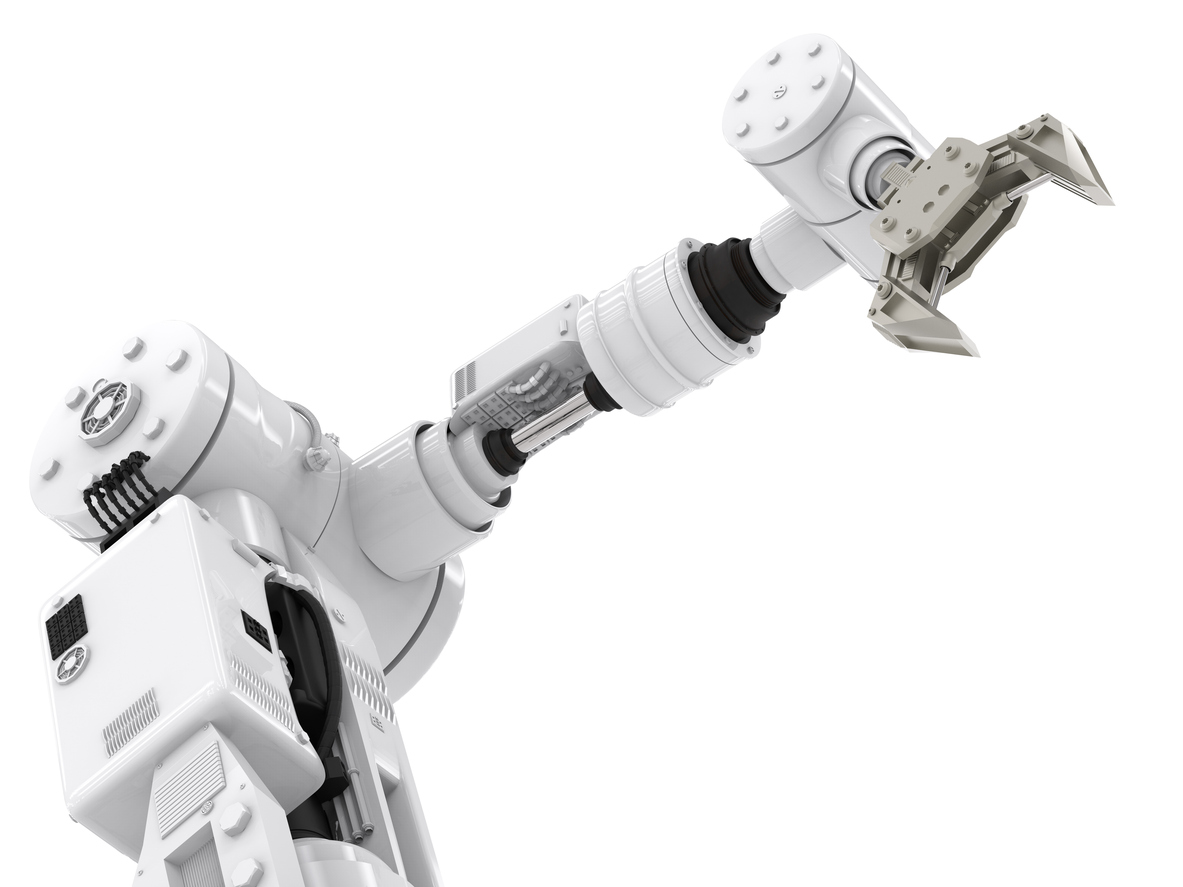
Industrial robots have revolutionized the manufacturing industry by significantly reducing cycle times in machine tending applications. By automating repetitive and time-consuming tasks, these robots not only increase productivity but also enhance precision and consistency. The key advantage of using industrial robots is their ability to perform tasks faster and more reliably than human operators, leading to a substantial improvement in overall efficiency.
One of the most significant benefits of robotic machine tending is its impact on a company’s bottom line. When implemented correctly, robotic systems can deliver a strong return on investment (ROI) by minimizing downtime, reducing labor costs, and increasing throughput. This makes them an essential component for manufacturers looking to stay competitive in today's fast-paced environment.
Key Features of an Effective Robotic Machine Tending System
To ensure long-term success, robotic machine tending systems must meet several critical performance criteria. These include:
- Accuracy: Precision is crucial in machine tending. A robot that can consistently pick and place parts without error reduces waste, rework, and production delays.
- Flexibility: Modern manufacturing often involves handling multiple part types. A good robotic system should be adaptable, allowing for quick tool changes and easy reprogramming for different tasks.
- Payload Capacity: Depending on the application, parts can be large and heavy. Therefore, the robot must have sufficient payload capacity to handle such components efficiently and safely.
- Speed and Reliability: High-speed operation combined with consistent performance ensures that cycle times remain low and production remains uninterrupted.
When these attributes are properly integrated into a robotic system, it can deliver measurable improvements in productivity and cost savings over time.
Real-World Success: Agricultural Manufacturer Cuts Cycle Time with Robotics
A case study from Genesis Systems Group highlights how robotics can transform machine tending processes. An agricultural manufacturer producing drive train components faced challenges with manual operations, which were slow and prone to errors. They needed a solution that could automate 16 different part numbers with minimal operator intervention.
The solution involved a single robot work cell equipped with dual 3-jaw grippers, a 180-degree indexing system, 2D vision, and red LED lighting. This setup enabled the robot to accurately and quickly tend machines, cutting the overall cycle time to under 60 seconds. The system maintained a high uptime of 95%, proving its reliability and efficiency.
This successful implementation helped the manufacturer eliminate inefficiencies, reduce labor costs, and achieve a strong ROI. It also demonstrated the power of automation in modern manufacturing environments.
If you're interested in learning more about this project or exploring how robotic machine tending can benefit your business, check out the full case study from Genesis Systems Group.
Posted in Robotic Machine Tendinghot work tool steel,hot work steels,hot work die steel,hot die steel h13
Jiangyou ChongxinSpecial Metal Materials Co., Ltd. , https://www.zhongxindiesteel.com