Product Description:
Business Type | Manufacturer (Customized CNC Machining Services),OEM CNC Machining,CNC Machinery,High precision CNC Machining,CNC Turning,Sheet metal fabrication,Die casting,Cold forging ,Heat Forging ,Customized metal parts |
Item Name | Â Manufacturing aluminum accessories for electrical&electronic products |
Materials Available | Stainless Steel: SS201, SS303, SS304, SS316 etc. Steel: Q235, 20#, 45# etc. Brass: C36000 (C26800), C37700 (HPb59), C38500( HPb58)tC27200(CuZn37), C28000(CuZn4 Iron: 1213, 12L14, 1215, etc. Bronze: C51000, C52100, C54400, etc. Aluminum: AI6061, AI6063, AL7075, AL5052, etc. Plastic: ABS, PC, PE, POW, Nylon, Teflon, PP. etc/as per you required. |
Processing | CNC Machining, CNC milling and turning,die casting,cold forging, grinding, bending, stamping, sheet metal fabrication,etc. |
Surface Treatment | bonding, sand blasting, buffering, anodizing, painting and assembling,Zinc-plated, nicke plated, chrome-plated, silver-plated, gold-plated,Passivation etc. |
Tolerance | ± 0.005mm |
Surface Roughness | Ra0.8-3.2 |
Drawing format | PDF/ DWG/ IGS/ IGES/STEP/ STP etc. |
Equipment | CNC Machines, CNC machining center, CNC turning, milling machines,three dimension measurement machine,etc. |
Capacity | 20,000 pieces per month |
MOQ | It depend on your design,small quantity accept |
QC System | 100% inspection before shipment |
Payment Term | T/T,L/C, Pay Pal, West Union |
Trade Terms | FOB. CIF, As per customers request |
Shipment Terms | 1)Â Â Â Â Â 0-100kg: air freight priority 2)Â Â Â Â Â > 100kg: sea freight priority 3)Â Â Â Â Â As per customized specifications |
Packaging Method | 1. Neutral packing (neutral plastic bag+ neutral carton) 2.      Custom packing ( with logo or barcode according to your requirement) |
Lead Time | 15-45 working days,it depend on your quantity |
Note | All parts are customized according to customer's drawings or samples. If you have any parts to be proterotype, please feel free to send your drawings/samples to us. |
FAQ
1)What Payment terms do you offer for international customer?
T/T,paypal ,west union or others
For product:50% deposit before production,50% before shipment.
For mould:full amount before production
2)What is your annual production capability ?
8 Millions-10 Millions US $
3)how many CNC machines do you have?
20 Brother CNC Machines
8 Cutting CNC
8 Milling CNC Machines
1 Three Dimension Measurement Machine
Auxilary equipment:Drilling machine, tapping machine, polishing machine and etc.
4)What is normal lead time?
Sample Lead time:3-7 working days(Without mould)
Mass Production:30 days.It depend on the Qty and the structure).
5)sample pictures of diffrent materials machining
See our showroom for your reference
6)surface treatment?
Ordinary anodic oxidation, hard anodic oxidation, rodin, chromate, SurTec, Buffering,Sand Blasting,Powder Coating,Painting,Hard Anodizing,Brushingelectrophoresis, spraying, electroplating, etching, laser, black passivation, pickling, QPQ, heat treatment, medium frequency, high frequency, nitride, carburizing, tempering, phosphating, magnetic force grinding, ultrasonic cleaning
7)what is your quality process
New drawings analysis - the internal production control conversion - drawing process flow chart - first manufacturing inspection - modified with numerical optimization - normal production - QC inspection record - surface treatment - FQC inspection report and record - packaging logistics
8)Do you measure details and attach measure protocoll with delivery?
Inspection report, material certificate, packing list and material details of label attached in the package.
quality control :
IPQC inspect each one during every step: 100% inspection before shipment by micrometer , height gauge , projector measuring machine , coordinate measuring machine etc . any disqualification should be avoid and solve by us before shipment .
advantages of cooperation with FTOP:
1,Rapid speed :we have more than 20 latest brother CNC machines Using the latest lathe machines and milling machines , FTOP produces highly accurate parts in just 1-10 days.
2,Scalability : CNC Machining is perfect for production of 1-1,000 parts.
3,Precision: Offers high-precision tolerances (+/- 0.001″) and easily reproducible processes.
4,Material Selection:CNC Machining offers a wide variety of certified materials.
5,Custom Finishes:Select from a variety of finishes on solid metal or plastic parts, built to precise design specific.
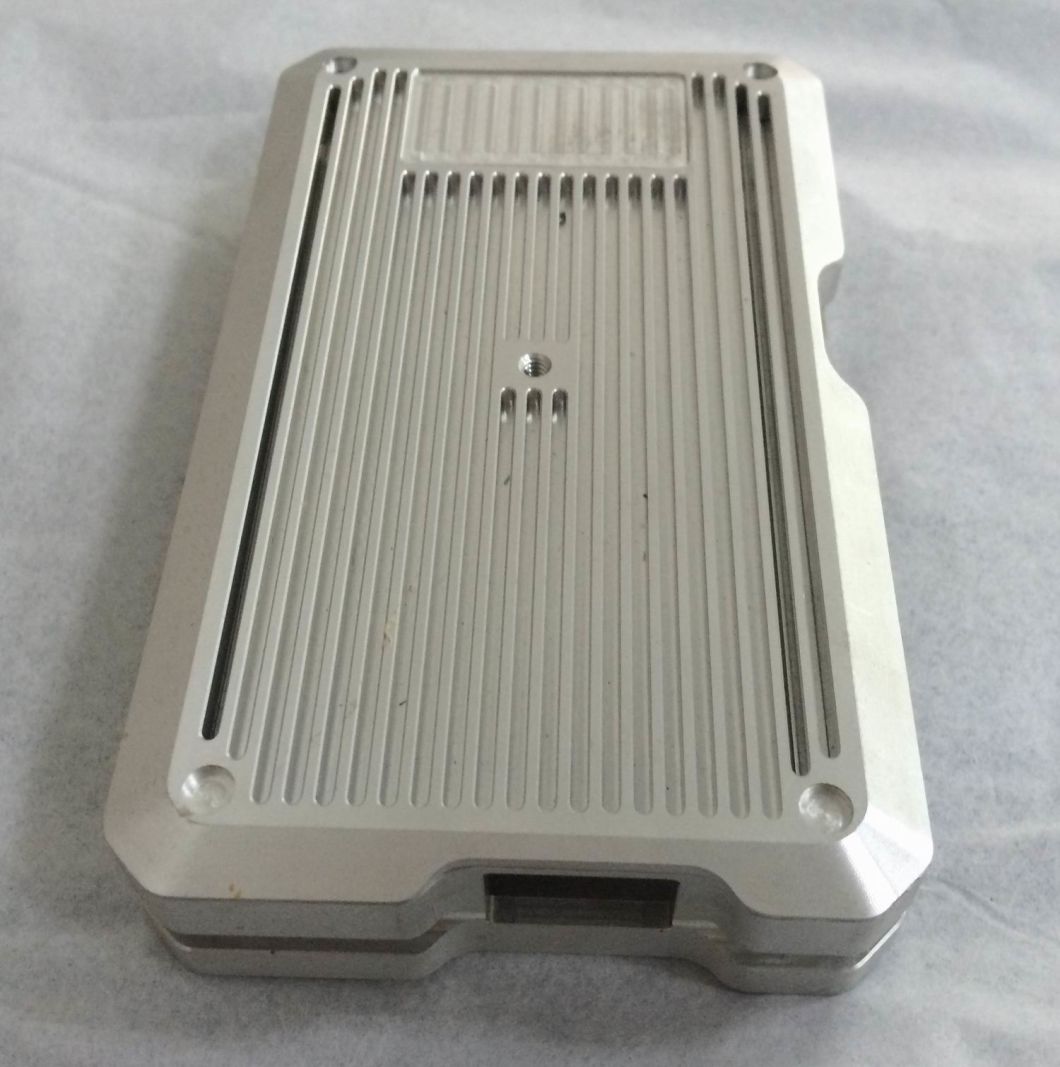
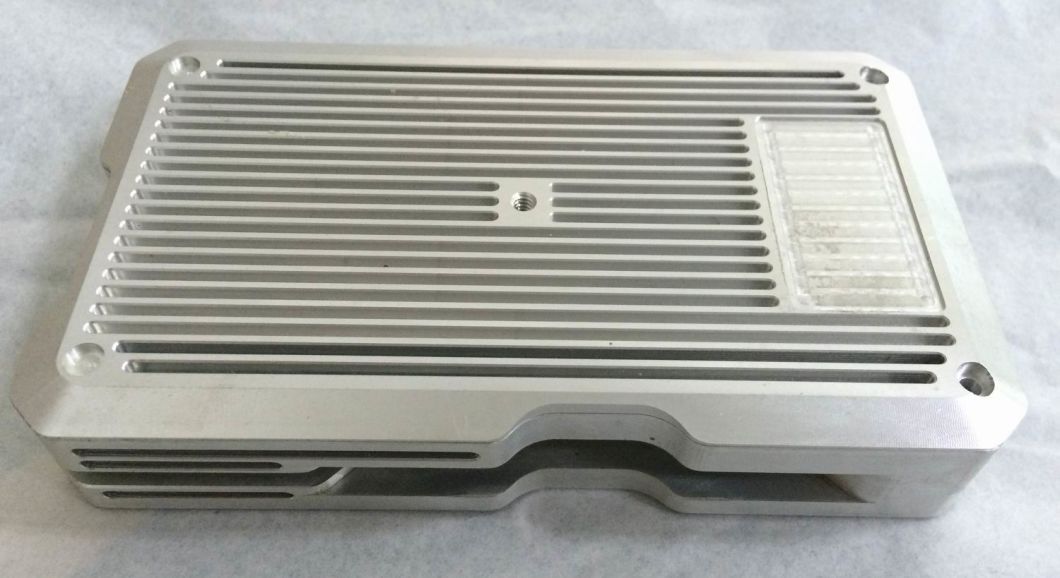
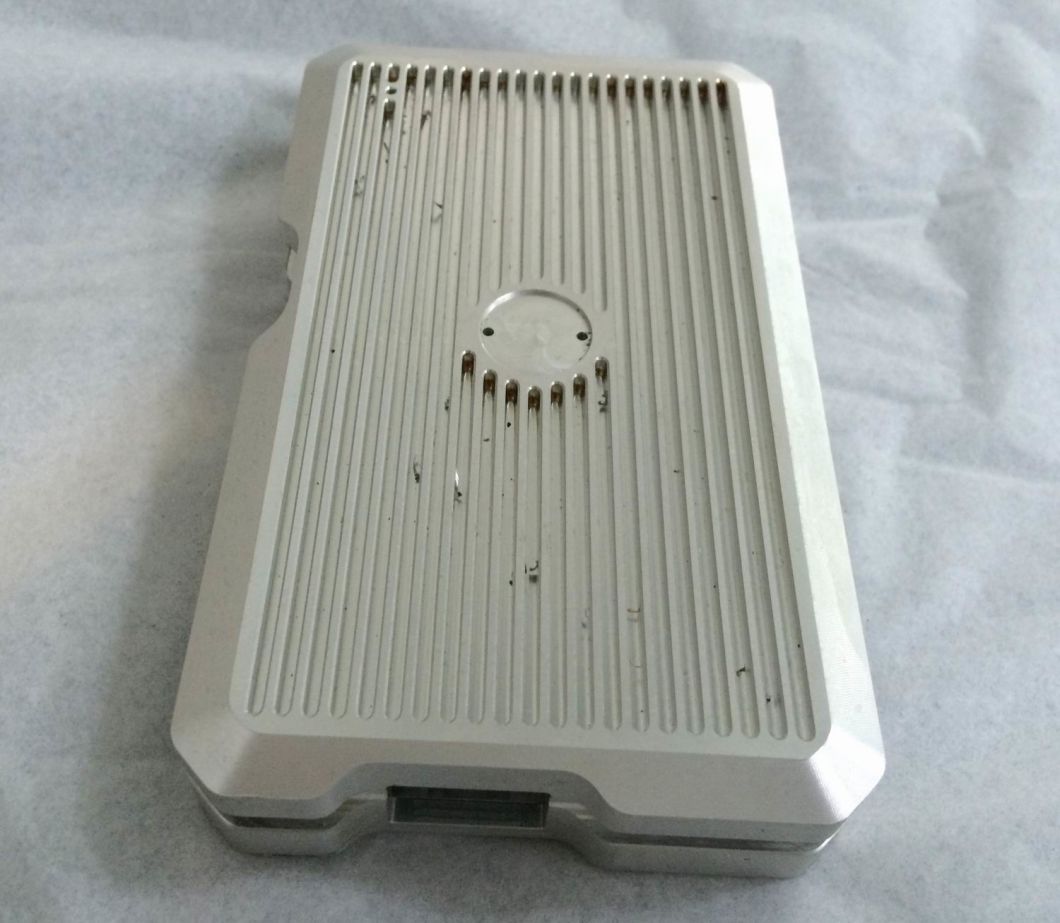
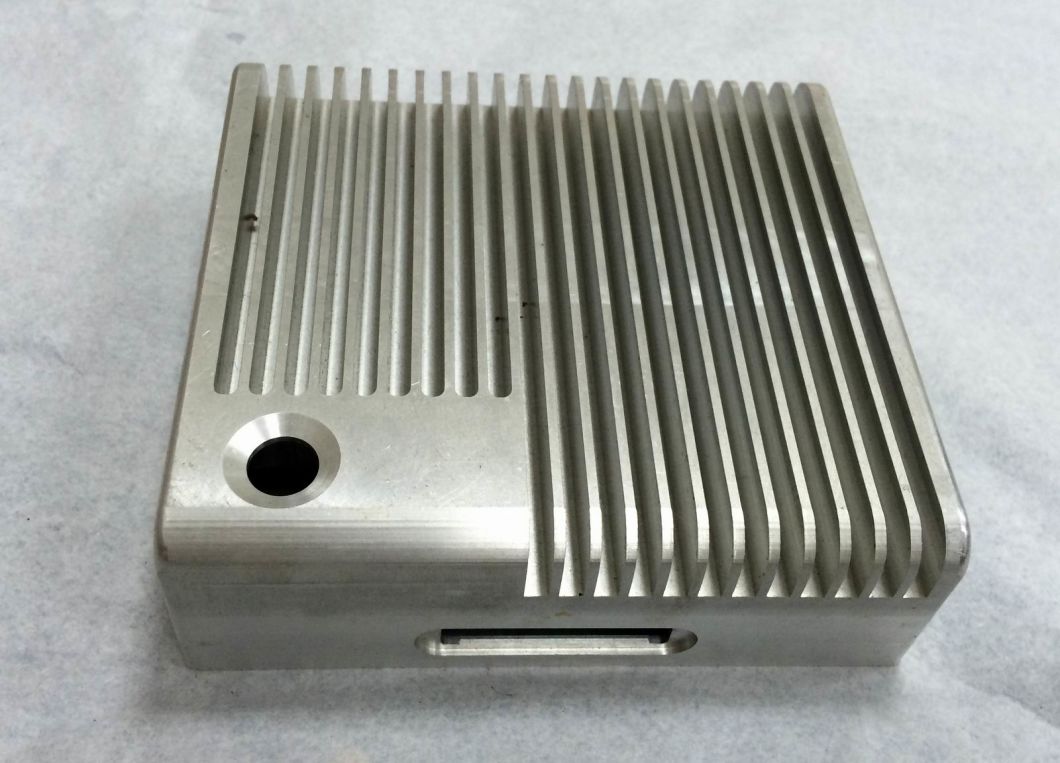
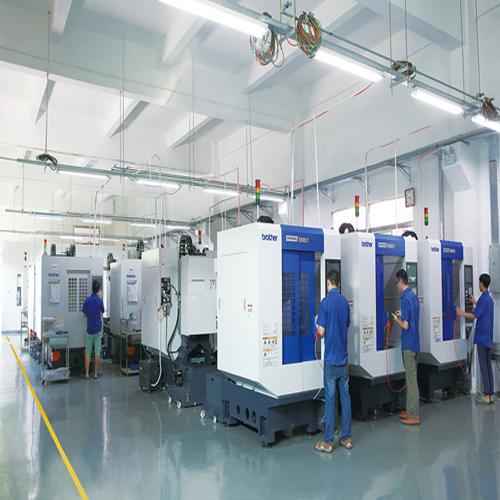
Shipping :
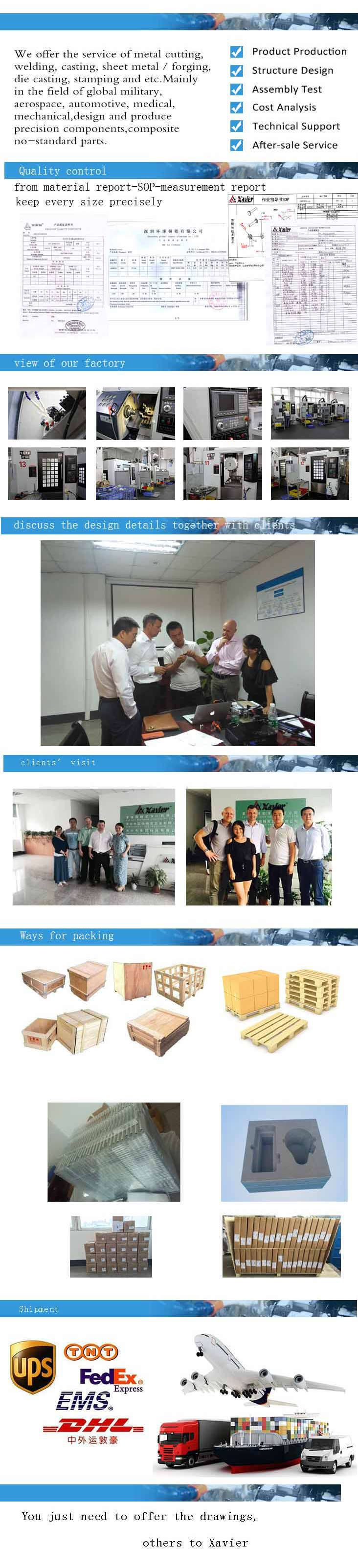
Â
Now every country optimistic about the prospect of the magnesium alloy die castings,especially in auto,aviation,telecom,transportation and mechanical industry,
which adopt to use magnesium alloy die casting to replace steel casting for reducing weight effectively and then can save energy and reduce environment pollution. The car can decrease 0.4L oil consumption per kilometer if it can relieve every 100KGS. So America,Japan and European countries have enlarge use of magnesium alloy Die Casting Parts, for example, steering wheel, instrument panel, seat skeleton, crankcase, gearbox shell, wheel hub and so on. So magnesium alloy die castings grows at 20%~30% a year, 80% of them are die casting parts. Meanwhile magnesium alloy die castings expand use in appliance light industry and daily hardware, such as notebook shell, VCR box, mobile phone, power tool shell,camera shell, upholstery, mower shell etc. These magnesium alloy die casting parts with a series of advantages, not only greatly reduce weight, but also have the precise & steady dimension and smooth finish surface.
Die-cast magnesium alloy material:
Magnesium and aluminum have big differences in the chemical, physical properties, mainly in terms of chemical reactivity, surface oxidation of the liquid metal
material tightness, thermal effects during solidification, resistant to electricity chemical corrosion resistance capabilities.
Magnesium has a strong chemical reactivity than aluminum and the metal bath surface can not be formed as dense as molten aluminum alloy oxide protective film
to prevent oxidation reaction to proceed, so magnesium alloy flammable or explosive. Magnesium alloy is also easy to dissolve other metals, including magnesium
alloy severely reduce the ability of anti-electrochemical corrosion of nickel, copper and other elements. In addition, the same volume of liquid aluminum and magnesium alloy during solidification.
Magnesium alloy heat release was significantly lower than aluminum.
Magnesium alloy chemical elements:
Mechanical properties of pure magnesium is very poor, can not meet the requirements of industrial parts of the yield strength and tensile strength. By adding alloying elements can significantly improve the mechanical properties of magnesium, the magnesium alloy`s strength to weight than the titanium alloy in all kinds of alloying and ranked second, open up broad prospects for its application.
The effect of alloying element second is to improve the performance of magnesium alloy casting. Pure magnesium have high melting point, poor mobility, high shrinkage.
By alloying can reduce the temperature of the liquid, increase liquidity. According to the characteristics of magnesium alloy decreased significantly at temperature above 150degrees Celsius and the strength of the alloy,
the third role is to enhance the creep resistance of magnesium alloy.
Magnesium alloy commonly used alloying elements are aluminum and zinc. Alloying of aluminum alloy can improve the strength and casting properties. Zinc can also improve the performance of the alloy casting. In order to ensure the casting performance, the aluminum content should be more than 3% in the die casting magnesium alloy, zinc content is less than 2%. Otherwise it is easy to produce crack.
The commonly used magnesium alloy die-casting material
Common cold chamber die casting machine injection parts must be improved to meet the needs of the magnesium alloy die casting production as follows:
1) Fast injection speed increased from 4~5m/s to 6~10m/s.
2) Reduce the time of supercharging and build pressure.
3) Improve the injection speed and injection force control.
4) Equipped with a special furnace protection gas device
The aluminum die casting part production flow chart
Commonly used materials of magnesium alloy die casting: ADC12, ZL101, ZL102,A380, AlSi9Cu3, AlSi12(Fe);
The precision of the magnesium die casting: ±0.1mm;
Smoothness of surface of rough part: Ra1.6~Ra3.2;
Shrinkage rate of Mg alloy die casting products: 0.5%;
Material wastage rate: 5%;
General magnesium die-casting machining allowance: 0.5mm~0.7mm;
Surface preparation methods: Sand blasted, Shot blasting, Powder coating, Painting, Plating, Electrophoresis, Polishing
Our company's magnesium alloy die casting production equipment and management system
Aluminum Die casting production equipment: L.K brand die casting machine From 160T, 200T, 280T, 400T, 630T, 800T and 1250T;
CNC machining center: 8 sets;
CNC lathe machine: 6 Guangzhou Machines and 7 Shenyang Machines;
Work days of one week: From Monday to Saturday;
Shift work: 2 shift per day;
Working hours: From AM 8:00 to PM 5:00;
2D and 3D drawing Software: AutoCAD, UG, Pro/E, SolidWorks 2013;
QC control: New type NANO CMM, FPI M5000 desktop metal analyzer, Easson projector, Mechanical properties tester.
The production of Magnesium die casting and QC control
Magnesium Die Casting Part, Magnesium Alloy Die Casting Part, Magnesium Die-Casting Product, Magnesium Injection Part
NINGBO BEILUN LEMA MACHINERY TECHNOLOGY CO.,LTD , http://www.china-lema.com