Cavity: 1-1, 1-2, 1-4
Insert: Alinimum, Copper, Sst, Steel Parts
Color: Full Range
Packaging: Carton
Lead Time: 2 Weeks
Tooling: Yes
Trademark: QIRUI
Transport Package: Carton
Specification: Customized
Origin: China
HS Code: 3917400000
Cavity: 1-1, 1-2, 1-4
Insert: Alinimum, Copper, Sst, Steel Parts
Color: Full Range
Packaging: Carton
Lead Time: 2 Weeks
Tooling: Yes
Trademark: QIRUI
Transport Package: Carton
Specification: Customized
Origin: China
HS Code: 3917400000
Plastic Injection Mold,Medical plastic products:Â It all begins with the mold. With decades of experience in building precision molds, we have the skills required to meet the most exacting of standards. That is for producing injection molded plastic components of the very highest quality and precision at highly competitive prices. You can be sure of excellence in all stages of design, tooling and manufacturing. Â
Plastic Injection molding is used to create many things such as wire spools, packaging, bottle caps, automotive dashboards, pocket combs, some musical instruments (and parts of them), one-piece chairs and small tables, storage containers, mechanical parts (including gears), and most other plastic products available today. plastic Injection molding is the most common modern method of part manufacturing; it is ideal for producing high volumes of the same object.Â
Plastic injection molding products sample
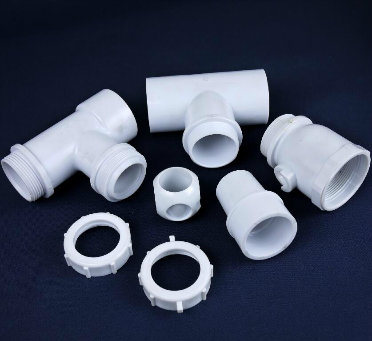



Â
Material | Specific gravity | Melting point  (°F) | Melting point  (°C) |
---|---|---|---|
Epoxy | 1.12 to 1.24 | 248 | 120 |
Phenolic | 1.34 to 1.95 | 248 | 120 |
Nylon | 1.01 to 1.15 | 381 to 509 | 194 to 265 |
Polyethylene | 0.91 to 0.965 | 230 to 243 | 110 to 117 |
Polystyrene | 1.04 to 1.07 | 338 | 170 |
 It all begins with the mold. With decades of experience in building precision molds, we have the skills required to meet the most exacting of standards. That is for producing injection molded plastic components of the very highest quality and precision at highly competitive prices. You can be sure of excellence in all stages of design, tooling and manufacturing. Â
Plastic Injection molding is used to create many things such as wire spools, packaging, bottle caps, automotive dashboards, pocket combs, some musical instruments (and parts of them), one-piece chairs and small tables, storage containers, mechanical parts (including gears), and most other plastic products available today. plastic Injection molding is the most common modern method of part manufacturing; it is ideal for producing high volumes of the same object.Â
Plastic injection molding products sample
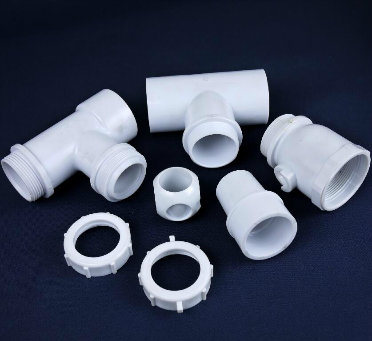



Â
Material | Specific gravity | Melting point  (°F) | Melting point  (°C) |
---|---|---|---|
Epoxy | 1.12 to 1.24 | 248 | 120 |
Phenolic | 1.34 to 1.95 | 248 | 120 |
Nylon | 1.01 to 1.15 | 381 to 509 | 194 to 265 |
Polyethylene | 0.91 to 0.965 | 230 to 243 | 110 to 117 |
Polystyrene | 1.04 to 1.07 | 338 | 170 |
Matting Agent For Economic Coatings
CAS 7631-86-9 SILICON DIOXIDE CHINESE SUPPLIER - QUANXU TECHNOLOGY
Silica (SiO2) in economical coating additives is a widely used inorganic filler. It plays a variety of roles in the coating industry and plays an important role in improving coating performance and reducing costs. The following are several main uses of silica in coating additives:
1. Enhance the mechanical properties of the coating: Silica particles can increase the hardness and wear resistance of the coating and improve the scratch resistance of the coating.
2. Improve leveling and hiding power: By adjusting the particle size and dispersion state of silica, the leveling of the coating can be effectively improved, while the hiding power of the coating can be improved and the amount of coating required can be reduced.
3. Adjust gloss: Silica of different particle sizes and forms can affect the gloss of the coating, thereby meeting the needs of different application scenarios.
4. Improve weather resistance and corrosion resistance: Silica as a filler in the coating can effectively block the damage of ultraviolet rays to the coating and enhance the weather resistance and corrosion resistance of the coating.
5. Reduce costs: Compared with some organic fillers or metal oxides, the cost of pure silica is relatively low. Using an appropriate amount of silica can reduce the production cost of coatings while ensuring performance.
6. Environmental protection: Silica is a natural non-toxic material that meets the requirements of modern coatings industry for environmental protection performance.
7. Auxiliary film-forming substance: In some specific coating systems, such as water-based coatings, silica can be used as an auxiliary film-forming substance to help form a stable coating structure.
In short, as an economical coating additive, silica plays an important role in improving coating performance, reducing costs, and protecting the environment. However, its specific application effect will be affected by factors such as coating formula and use conditions. Therefore, in actual applications, it is necessary to make appropriate selections and adjustments according to specific needs.
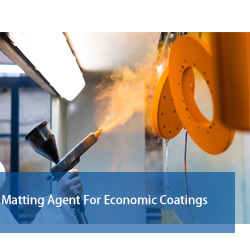
Economic Paint Agent Silica Dioxide, 7631-86-9 Precipitated Silicon Dioxide, CAS 7631-86-9 Matting Powder
Guangzhou Quanxu Technology Co Ltd , https://www.skyelecteflonheater.com