Model NO.: CTCS
Pressure Loss: 0.003MPa-0.05MPa
Characteristic: Easy to Operate,Saving Space and Covering Less Are
Optional Chemical Dosing System: Prevent Corrosion of Tubes and Save Water
Trademark: PEIDE
Transport Package: Wooden Case
Specification: Carbon Steel, 304ss or 316L
Origin: China
Model NO.: CTCS
Pressure Loss: 0.003MPa-0.05MPa
Characteristic: Easy to Operate,Saving Space and Covering Less Are
Optional Chemical Dosing System: Prevent Corrosion of Tubes and Save Water
Trademark: PEIDE
Transport Package: Wooden Case
Specification: Carbon Steel, 304ss or 316L
Origin: China
Chiller auto condenser tube cleaning system
Â
Â
Introduction to condenser tube cleaning system   Â
Condenser tube cleaning system is a device used to scrub the inner wall of heat transfer tubes of central air-conditioner condenser by physical method.When the central air-conditioner is in refrigeration process,the temperature of the refrigerant rises,so it must be lowered.Cooling water system is the pipeline system used for cooling down the refrigerant and the condenser is the heat-exchange device for cooling refrigerant.Cooling water flows into the condenser through the inner wall of the heat transfer tubes and then flows out.The cooling refrigerant flows through the outer wall of the heat transfer tubes and the condenser exchanges heat by heat transfer tubes,and thus cool down the refrigerant.The cooling water flows into the condenser at a low temperature and flows out at a high temperature after absorbing heat.After operating for a long time,the heat transfer tubes may have incrustation,fouling and stain sediment on inner wall,which may affect the heat transfer efficiency.Small temperature drop of the refrigerant affects the refrigeration effect, increases the load on the host of the central air-conditioner and reduces the life of it,so the inner wall of the condenser heat transfer tubes must be regularly cleaned to extend the life of it.
On-line condenser cleaning system is a kind of equipment used for automatically cleaning the inner wall of the condenser heat transfer tubes on line by physical method when the refrigerating unit is under operation.By injecting and collecting the balls,the system can clean the heat transfer tubes periodically.This system can reduce usage amount of water treatment chemicals,enhance refrigerating efficiency of the unit and save electric energy.
Â
Operating principle of condenser tube cleaning system
To start with the water pump of the condenser tube cleaning system and pump the balls from the ball injector to the water inlet of the condenser with water.The balls enter the end cover of the condenser along with the circulating cooling water and get into the copper tube of the condenser randomly.Driven by the circulating cooling water,the balls move inside the copper tube to scrub the inner wall of the tube.After leaving the tube,the balls get out of the end cover of the condenser with the circulating cooling water and enters the ball collector installed on the outlet pipeline of the condenser.Ball trap in the ball collector then traps the balls,with the water flowing away through the screen.Then the balls return to the ball injector,which means a whole cleaning process is finished.The cleaning frequency and times can be set via microcomputer control program,to realize automatic on-line cleaning.
Control mode of condenser tube cleaning system
Automatic control:Set cleaning frequency and times via microcomputer control program,to realize automatic on-line cleaning.
Manual control: Manually start the condenser tube cleaning system.
System composition of condenser tube cleaning system
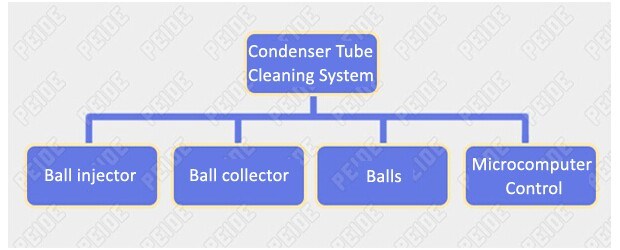
Ball injector:The container used for storage,injecting and collecting balls.The installation position of the ball injector and the inlet and outlet connecting pipes shall ensure that the balls are even without blockage.
Ball collector:When the balls leave the condenser,they'll be caught by the ball collector.The chamber material is carbon steel or stainless steel,the max working pressure is 10-25 bar,the effective open area is greater than 3 times of that of the connecting pipe and the hydraulic resistance loss is less than 5 Kpa.The ball collecting screen shall be designed with good hydraulic characteristics to prevent the screen from vibrating under the impact of water flow.The design of the ball collecting screen shall ensure no blocking or slipping of balls.
Sponge balls:Used for cleaning inner wall of the condenser heat transfer tubes.The balls shall have uniform density and good recoverability.When the balls work at a water temperature of 5-36 ºC,the diameter of wet balls shall not be larger than 0.5 mm of dry balls.During the operation,the diameter of the balls shall be 1-2 mm larger than the inner diameter of the heat transfer tubes.The balls shall remain stable during the operation to prevent the blocking of cooling water pipe.
Specification for balls and adaptive inner diameters of copper tube to be cleaned
Inner diameters of copper tube (mm) |
16 | 17 | 18 | 19 | 20 | 21 | 22 | 23 | 24 | 25 |
Diameters of balls (mm) | 17 | 18 | 19 | 20 | 21 | 22 | 23 | 24 | 25 | 26 |
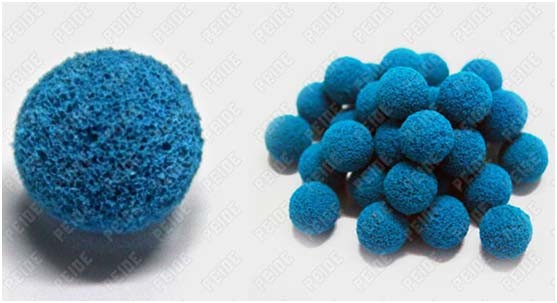
Microcomputer controller:Automatically control and set cleaning frequency and time.It can also be set according to temperature difference of the water getting in and out of the condenser to trigger cleaning.
Â
Problems resulted from scaling in copper tube of condenser
Scaling on tube wall reduces the surface heat transfer efficiency and affects the heat transfer coefficient of tube.
After using the condenser tube cleaning system, the heat transfer coefficient of tube can be maintained at the system initial state.
1 mm thick accumulated scaling in tube of condenser will increase 30% of energy consumption.
After using the condenser tube cleaning system,the host energy consumption can be maintained at a utilization of 100%.
Functions of condenser tube cleaning system
Improve operating efficiencyÂ
Since condenser tube cleaning system that enables copper tube of condenser to get rid of scaling and operation of compressor will not exceed the design limit,the central air-conditioner can operate at its optimum efficiency.
Extend service life of central air-conditioner and reduce maintenance
Since operation of compressor will not exceed its design limit, life of equipment is extended, and thus effectiveness and investment return of the central air-conditioner are enhanced. Yet certain maintenance is still necessary.
Reduce overall energy consumption
When the compressor operates at the maximum power,the central air-conditioner can generate the same output by consuming less energy.In a typical case,the energy saving department of a semiconductor manufacturer audited the condition before and after installing the condenser tube cleaning system for a 800 tons central air-conditioner and found that it saved energy amounting to 83,000 USD every year by using condenser tube cleaning system and investment payback period is 4 months.
Reduce the cost of water treatment
Since the condenser tube cleaning system enables the copper tube of the condenser to get rid of scaling,the water treatment just needs some auxiliary equipment to prevent scaling,such as cooling tower and valves,etc.An independent audit of manufacturer found that,after installing the condenser tube cleaning system,the cost of the chemicals used for treating water had reduced by 51%.In another audit of a commercial building with two 300 tons central air-conditioners,the total hardness and total dissolved solids had reduced by 51% and 53% respectively.
Prevent corrosion of condenser tube
Microbiological corrosion and centralized cell corrosion results from scaling on tube wall.Since the condenser tube cleaning system can prevent tube scaling,these corrosion mechanisms will be eliminated,thus extending the service life of the tube.
Comparison between condenser tube cleaning system and traditional descaling methods
Â
Performance Approach | Chemical + Mechanical Cleaning | condenser tube cleaning system |
Cleaning method | Chemical/Manual | Automatic/Physical |
Cleaning of scale and fouling | Temporary cleaning | Obvious and stable effect |
Cleaning of biological film | Temporary and partial effect | Good |
Bacteria and algae prevention | Produce legionella and need Other bactericidal chemicals | Good |
Environmental pollution | Serious for producing high-concentration hazardous chemical water pollution | None |
Damage to the equipment | Corrode and wear the equipment | None |
Cleaning costs | High | None |
Restrictions | The host needs to be shut down. | None |
Benefit analysis of condenser tube cleaning system
For instance,there is a central air-conditioner with 3 chillers,each of which has a compressor power of 429KW and operates throughout the years.In summer,all three chillers will be under operation,with a total compressor power of 1287 KW and an operation time of 4 months.In other seasons,two chillers will be under operation,with a total compressor power of 858 KW and an operation time of 6 months.Since water quality varies in different regions,the energy saving effect is various between 15%-35%.Assume the energy saving rate is 0%,the average load is 80%,the chillers operates for 24 hours per day and 30 days per month and the electric charge is RMB 1.0 per kw/h,
Then: The electric charge saved per month in summer is:
1287 kW×80%×1 h×1.0 RMB/ kw/h×20%×24 h×30 days= RMB 148262.4.
And the electric charge saved per month in other seasons is:
858 kW×80%×1 h×1.0 RMB/ kw/h×20%×24 h×30 days= RMB 98841.6.
The electric charge saved in the whole year is:
RMB 148262.4×4 months +RMB 98841.6×6 months=RMB 1186099.2
In addition,the total economic benefit reaches as much as 1.2 million yuan per year,including the expenses on chemical cleaning,labor and equipment maintenance,and calculated at an available machine year of 10 months per year.As it turns out,the user can recover the investment cost of the equipment in a short time.
Features of condenser tube cleaning system
1. The host of condenser tube cleaning system integrates the water pump and ball injector,saving space and covering less area.
2. It's easy to operate.The cleaning can be finished by controlling the start and stop of the water pump by time,and the cleaning time,interval and frequency can be set.
3. The ball collector is equipped with a water flow switch.When the circulating cooling water stays still,the water pump of the cleaning device cannot rotate,which prevents the water pump from operating without water.
4. The ball collecting screen applies stainless steel screen with large mesh size,which only traps the balls and has low water resistance.
5. The balls only circulate in the pipeline and do not go through water pump,which can prevent the pump impellers from hitting the balls and extend the service life of the balls.
6. The operating cost is low and the sponge balls are the only consumables.
Comparison before and after using the condenser tube cleaning system
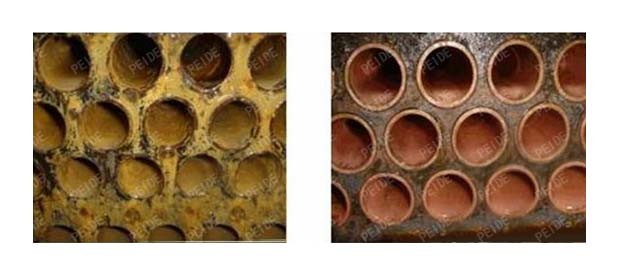
                  Before cleaning                           After cleaning
Application of condenser tube cleaning system
Applicable for the following high energy consumption systems:Non cooling refrigeration equipment;constant temperature and constant humidity control system;and marine water cooling system;
Supporting facilities:Mansions,hotels,malls,banks,hospitals and other public utilities;
Refrigeration facilities:Chained supermarket and cold stores;
Chemical factories:Cooling system on production lines;
Manufacturers of electronic parts and components,semiconductor integrated circuits and liquid crystal displays,etc;
Specification parameters of condenser tube cleaning system
1. Performance index: Ball collection rate ≥99%
2. Input voltage:380V/50HZ (provide customization as required)
3. Power: ≤4KW
4. Requirements for working environment: Temperature ≤55ºC, relative humidity ≤95ºC
5. Pressure loss: 0.003MPa-0.05MPa
6. Applicable water temperature: ≤50ºC
7. Working pressure: ≤1.6MPa (customization for 2.5Mpa)
How to choose the type of condenser tube cleaning system
1.The design and selection of condenser tube cleaning system is determined by the refrigerating capacity of the chillers and the outlet pipe diameter of the cooling water.The size of balls shall be decided by the inner diameter of condenser heat transfer tubes of cold water host.
2.In order to prevent welding slags,welding rods,metal debris,sand and organic fabrics in the installation process,and the filling of cooling tower,corrosion in the cooling tubes and other foreign materials in the operation process from entering the condenser and evaporator,a less than 1.5mm precision of filter shall be installed in front of water inlet of chiller condenser (evaporator) and the effective filtering area of filter screen shall be 3 times larger than section area of the connecting pipe,to ensure proper water resistance of the filter.
Model code for condenser tube cleaning system
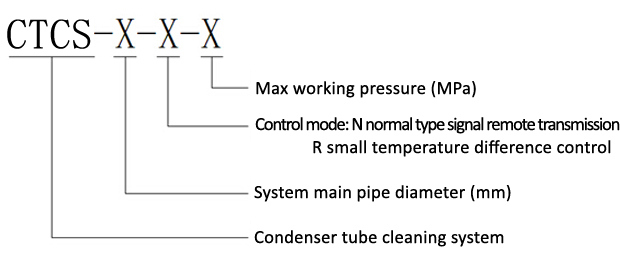
Specifications and models of condenser tube cleaning system
No. | Model | Selection guide, subject to actual cooling water pipe diameter |
1 | CTBC-150-N-1.6 | General host under 200 RT |
2 | CTBC-200-N-1.6 | General host between 200-500 RT |
3 | CTBC-250-N-1.6 | General host between 300-500 RT |
4 | CTBC-300-N-1.6 | General host between 500-800 RT |
5 | CTBC-350-N-1.6 | General host between 600-1000 RT |
6 | CTBC-400-N-1.6 | General host between 1000-1500 RT |
7 | CTBC-450-N-1.6 | General host above 1500 RT |
Installation diagram of condenser tube cleaning system
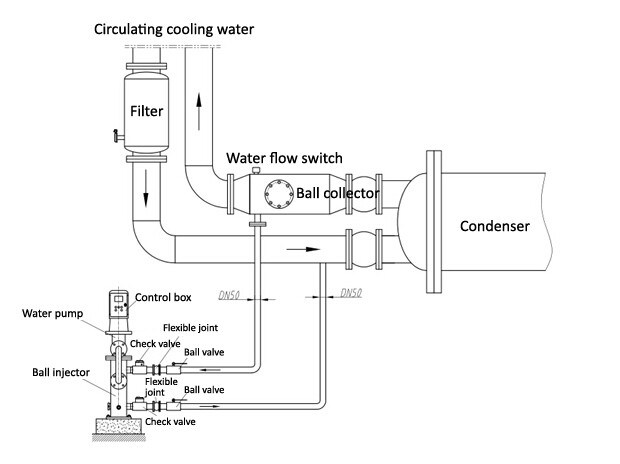
Precautions for Installation of condenser tube cleaning system
1.Connect the pipelines according to the pipeline system diagram and avoid incorrect connection.
2.Connect the injecting mouth of ball injector to the opening DN50 on the water inlet pipe of the condenser near the end cover,and install the DN50 ball valve on pipeline.The opening must be located behind the filter.
3.Install the ball collector on the water outlet pipe of condenser.Connect the DN50 flange outlet of ball collector to collecting mouth of ball injector and install a DN50 ball valve on pipeline.The host of condenser tube cleaning system shall be located near the condenser as much as possible.
4.The pipeline shall be simple so as to reduce the pipe bending and pipe length.
5.To ensure there is no welding slag,scrap iron or other things in the pipe from the injecting point on water inlet pipe of condenser to collecting point of ball collector or the end cover of condenser, so that the balls can clean the heat transfer tubes without being blocked or scratched by foreign materials.It is suggested to install the filter in front of injecting point on the water inlet pipe of the condenser.
6.Reserve a maintenance space of 0.6 m around the host of condenser tube cleaning system. Connect the water flow switch and the electrically operated valve of the filter according to the number.The control box applies a power supply of 380V/50Hz.Notice that the rotation arrow of water pump shall be consistent with that of water pump identification.
Compared with other suppliers for condenser tube cleaning system
Â
Project | PEIDE | Other suppliers | Note |
Covered area | Small, quarter of other suppliers | large | required to cover a small area due to the small room space |
Pipeline connection | two Ball valves, two soft connectors, one pipeline, easy and convenient | four ball valves, four soft connectors, two pipelines | easy to install due to the simple pipeline, Low installation cost |
Equipment reliability | PEIDE has proprietary technology,Pure mechanical structure design,no electrical action parts except the water pump, reducing the failure | three or four electric valve,easy to cause electrical failure |
Because the electric valve needs to be adjusted after using for a period of time, To ensure the valve closed  totally. |
Maintenance | The electronic control part adopts a modular control unit.Faulty direct replacement. | Discrete devices,not easy to judge the fault.Need professional maintenance. | Â |
Energy efficiency | Reduce air-conditioning running costs by 6-12% | Reduce air conditioning running costs by 0-2% | Energy-saving efficiency depends on the ball collection rate |
Acceptance check |
10% savings in central air-conditioning electricity due to good product performance. No additional fees for equipment acceptance. |
Due to the bad effect of the ball collection rate.There is an additional fee for equipment acceptance. Even failed in acceptance,resulting in difficulties in getting balance payment. |
 |
Site pictures of some cases of condenser tube cleaning system
CASE 1
Application:Cleaning condenser of central air-conditioning system of mansion of bank of communications
Client:Shanghai Branch,Bank of Communications
Core advantages:Simple and convenient to install and maintain and less maintenance
Brief introduction:
Main pipe diameter of applicable system: DN300
Inlet and outlet diameter: DN50
Chamber material: carbon steel
Max working pressure: 1.0MPa
Installed with air exhausting device and drainage device as well as ball adding and placing device
Inlet and outlet diameter of ball collector: DN300
Chamber material: carbon steel
Material of ball collecting filter screen: 304 stainless steel
Set with access hole and pressure gauge indicating the pressure difference before and after the filtering screen of ball collector
Max working pressure: 1.0MPa
Project profile: The project covers a land area of 1,908 m2 and a building area of 10,088 m2.
CASE 2
Application: Condenser cleaning of central air-conditioner
Client: Gree Industrial Park in Hefei,Anhui
Core advantages: Simple and convenient to install and maintain and less maintenance
Brief introduction:
CTBC-300-N-1.6 2sets
Main pipe diameter of applicable system: DN300
Inlet and outlet diameter of the ball injector: DN50
Chamber material: carbon steel
Max working pressure: 1.6 MPa
Installed with air exhausting device and drainage device as well as ball adding and placing device
Ball collecting and injecting pump: Flow: 8L/S
Lift:>20 m
Power: 4Kw
Inlet and outlet diameter of ball collector: DN300
Chamber material: carbon steel
Material of ball collecting filter screen: 304 stainless steel
Set with access hole and pressure gauge indicating the pressure difference before and after the filtering screen of the ball collector
Max working pressure:1.6 MPa
Automatic time control,adjustable cleaning frequency according to actual condition,manual control and malfunction alarm
Project profile:This project has a total investment of about RMB 4.4 billion and covers an area of about 1,525mu.It is the largest professional air-conditioner production base in Central and East China and the third largest in China.
CASE 3
Application: Cleaning of circulating water condenser
Client: ZhongyuDuhui Square
Core advantages: Simple and convenient to install and maintain and requiring less maintenance
Brief introduction:
CTBC-450-N-1.6 8sets
Main pipe diameter of applicable system: DN450
Inlet and outlet diameter of the ball injector: DN50
Chamber material: carbon steel
Max working pressure: 1.6 MPa
Installed with air exhausting device and drainage device as well as ball adding and placing device
Flow of ball collecting and injecting pump: 8L/S
Lift:>20 m
Power: 4Kw
Inlet and outlet diameter of the ball collector: DN450
Chamber material: carbon steel
Material of ball collecting filter screen: 304 stainless steel
Set with access hole and pressure gauge indicating the pressure difference before and after the filtering screen of ball collector
Max working pressure: 1.0 MPa
Automatic time control,adjustable cleaning frequency according to actual condition,manual control,malfunction alarm and PLC control
Project profile:With a total building area of over 400 thousand m2,this project is a large urban complex integrating 89 thousand m2 of youth experiencing shopping center,3 class-A office buildings and 1 ultra five-star hotel.It has about 2,200 parking spaces and 3 ultra-large outdoor squares.Its first floor underground leads to Jiazhoulu Station of Railway Line No. 3.
Packaging picture of condenser tube cleaning system
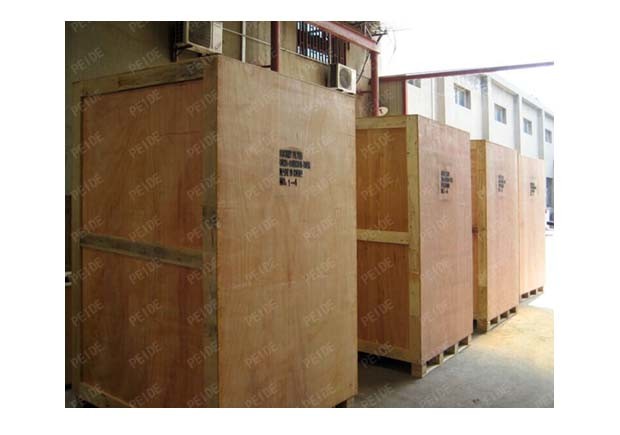
                Welcome To Inquire ,We Will Offer You The Best Items !
Chiller auto condenser tube cleaning system
Â
Â
Introduction to condenser tube cleaning system   Â
Condenser tube cleaning system is a device used to scrub the inner wall of heat transfer tubes of central air-conditioner condenser by physical method.When the central air-conditioner is in refrigeration process,the temperature of the refrigerant rises,so it must be lowered.Cooling water system is the pipeline system used for cooling down the refrigerant and the condenser is the heat-exchange device for cooling refrigerant.Cooling water flows into the condenser through the inner wall of the heat transfer tubes and then flows out.The cooling refrigerant flows through the outer wall of the heat transfer tubes and the condenser exchanges heat by heat transfer tubes,and thus cool down the refrigerant.The cooling water flows into the condenser at a low temperature and flows out at a high temperature after absorbing heat.After operating for a long time,the heat transfer tubes may have incrustation,fouling and stain sediment on inner wall,which may affect the heat transfer efficiency.Small temperature drop of the refrigerant affects the refrigeration effect, increases the load on the host of the central air-conditioner and reduces the life of it,so the inner wall of the condenser heat transfer tubes must be regularly cleaned to extend the life of it.
On-line condenser cleaning system is a kind of equipment used for automatically cleaning the inner wall of the condenser heat transfer tubes on line by physical method when the refrigerating unit is under operation.By injecting and collecting the balls,the system can clean the heat transfer tubes periodically.This system can reduce usage amount of water treatment chemicals,enhance refrigerating efficiency of the unit and save electric energy.
Â
Operating principle of condenser tube cleaning system
To start with the water pump of the condenser tube cleaning system and pump the balls from the ball injector to the water inlet of the condenser with water.The balls enter the end cover of the condenser along with the circulating cooling water and get into the copper tube of the condenser randomly.Driven by the circulating cooling water,the balls move inside the copper tube to scrub the inner wall of the tube.After leaving the tube,the balls get out of the end cover of the condenser with the circulating cooling water and enters the ball collector installed on the outlet pipeline of the condenser.Ball trap in the ball collector then traps the balls,with the water flowing away through the screen.Then the balls return to the ball injector,which means a whole cleaning process is finished.The cleaning frequency and times can be set via microcomputer control program,to realize automatic on-line cleaning.
Control mode of condenser tube cleaning system
Automatic control:Set cleaning frequency and times via microcomputer control program,to realize automatic on-line cleaning.
Manual control: Manually start the condenser tube cleaning system.
System composition of condenser tube cleaning system
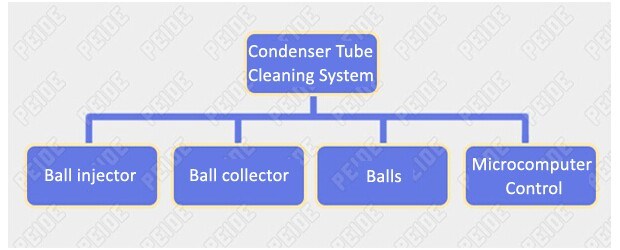
Ball injector:The container used for storage,injecting and collecting balls.The installation position of the ball injector and the inlet and outlet connecting pipes shall ensure that the balls are even without blockage.
Ball collector:When the balls leave the condenser,they'll be caught by the ball collector.The chamber material is carbon steel or stainless steel,the max working pressure is 10-25 bar,the effective open area is greater than 3 times of that of the connecting pipe and the hydraulic resistance loss is less than 5 Kpa.The ball collecting screen shall be designed with good hydraulic characteristics to prevent the screen from vibrating under the impact of water flow.The design of the ball collecting screen shall ensure no blocking or slipping of balls.
Sponge balls:Used for cleaning inner wall of the condenser heat transfer tubes.The balls shall have uniform density and good recoverability.When the balls work at a water temperature of 5-36 ºC,the diameter of wet balls shall not be larger than 0.5 mm of dry balls.During the operation,the diameter of the balls shall be 1-2 mm larger than the inner diameter of the heat transfer tubes.The balls shall remain stable during the operation to prevent the blocking of cooling water pipe.
Specification for balls and adaptive inner diameters of copper tube to be cleaned
Inner diameters of copper tube (mm) |
16 | 17 | 18 | 19 | 20 | 21 | 22 | 23 | 24 | 25 |
Diameters of balls (mm) | 17 | 18 | 19 | 20 | 21 | 22 | 23 | 24 | 25 | 26 |
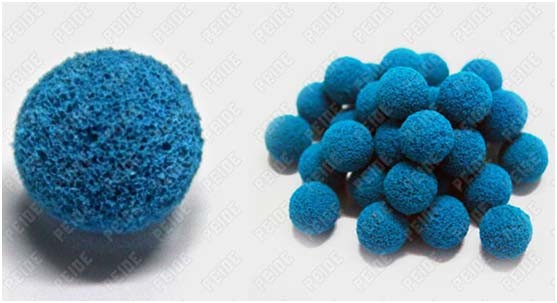
Microcomputer controller:Automatically control and set cleaning frequency and time.It can also be set according to temperature difference of the water getting in and out of the condenser to trigger cleaning.
Â
Problems resulted from scaling in copper tube of condenser
Scaling on tube wall reduces the surface heat transfer efficiency and affects the heat transfer coefficient of tube.
After using the condenser tube cleaning system, the heat transfer coefficient of tube can be maintained at the system initial state.
1 mm thick accumulated scaling in tube of condenser will increase 30% of energy consumption.
After using the condenser tube cleaning system,the host energy consumption can be maintained at a utilization of 100%.
Functions of condenser tube cleaning system
Improve operating efficiencyÂ
Since condenser tube cleaning system that enables copper tube of condenser to get rid of scaling and operation of compressor will not exceed the design limit,the central air-conditioner can operate at its optimum efficiency.
Extend service life of central air-conditioner and reduce maintenance
Since operation of compressor will not exceed its design limit, life of equipment is extended, and thus effectiveness and investment return of the central air-conditioner are enhanced. Yet certain maintenance is still necessary.
Reduce overall energy consumption
When the compressor operates at the maximum power,the central air-conditioner can generate the same output by consuming less energy.In a typical case,the energy saving department of a semiconductor manufacturer audited the condition before and after installing the condenser tube cleaning system for a 800 tons central air-conditioner and found that it saved energy amounting to 83,000 USD every year by using condenser tube cleaning system and investment payback period is 4 months.
Reduce the cost of water treatment
Since the condenser tube cleaning system enables the copper tube of the condenser to get rid of scaling,the water treatment just needs some auxiliary equipment to prevent scaling,such as cooling tower and valves,etc.An independent audit of manufacturer found that,after installing the condenser tube cleaning system,the cost of the chemicals used for treating water had reduced by 51%.In another audit of a commercial building with two 300 tons central air-conditioners,the total hardness and total dissolved solids had reduced by 51% and 53% respectively.
Prevent corrosion of condenser tube
Microbiological corrosion and centralized cell corrosion results from scaling on tube wall.Since the condenser tube cleaning system can prevent tube scaling,these corrosion mechanisms will be eliminated,thus extending the service life of the tube.
Comparison between condenser tube cleaning system and traditional descaling methods
Â
Performance Approach | Chemical + Mechanical Cleaning | condenser tube cleaning system |
Cleaning method | Chemical/Manual | Automatic/Physical |
Cleaning of scale and fouling | Temporary cleaning | Obvious and stable effect |
Cleaning of biological film | Temporary and partial effect | Good |
Bacteria and algae prevention | Produce legionella and need other bactericidal chemicals | Good |
Environmental pollution | Serious for producing high-concentration hazardous chemical water pollution | None |
Damage to the equipment | Corrode and wear the equipment | None |
Cleaning costs | High | None |
Restrictions | The host needs to be shut down. | None |
Benefit analysis of condenser tube cleaning system
For instance,there is a central air-conditioner with 3 chillers,each of which has a compressor power of 429KW and operates throughout the years.In summer,all three chillers will be under operation,with a total compressor power of 1287 KW and an operation time of 4 months.In other seasons,two chillers will be under operation,with a total compressor power of 858 KW and an operation time of 6 months.Since water quality varies in different regions,the energy saving effect is various between 15%-35%.Assume the energy saving rate is 0%,the average load is 80%,the chillers operates for 24 hours per day and 30 days per month and the electric charge is RMB 1.0 per kw/h,
Then: The electric charge saved per month in summer is:
1287 kW×80%×1 h×1.0 RMB/ kw/h×20%×24 h×30 days= RMB 148262.4.
And the electric charge saved per month in other seasons is:
858 kW×80%×1 h×1.0 RMB/ kw/h×20%×24 h×30 days= RMB 98841.6.
The electric charge saved in the whole year is:
RMB 148262.4×4 months +RMB 98841.6×6 months=RMB 1186099.2
In addition,the total economic benefit reaches as much as 1.2 million yuan per year,including the expenses on chemical cleaning,labor and equipment maintenance,and calculated at an available machine year of 10 months per year.As it turns out,the user can recover the investment cost of the equipment in a short time.
Features of condenser tube cleaning system
1. The host of condenser tube cleaning system integrates the water pump and ball injector,saving space and covering less area.
2. It's easy to operate.The cleaning can be finished by controlling the start and stop of the water pump by time,and the cleaning time,interval and frequency can be set.
3. The ball collector is equipped with a water flow switch.When the circulating cooling water stays still,the water pump of the cleaning device cannot rotate,which prevents the water pump from operating without water.
4. The ball collecting screen applies stainless steel screen with large mesh size,which only traps the balls and has low water resistance.
5. The balls only circulate in the pipeline and do not go through water pump,which can prevent the pump impellers from hitting the balls and extend the service life of the balls.
6. The operating cost is low and the sponge balls are the only consumables.
Comparison before and after using the condenser tube cleaning system
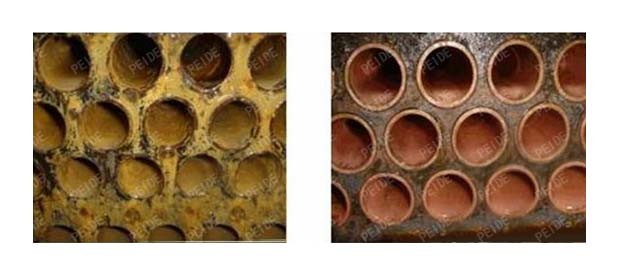
                  Before cleaning                           After cleaning
Application of condenser tube cleaning system
Applicable for the following high energy consumption systems:Non cooling refrigeration equipment;constant temperature and constant humidity control system;and marine water cooling system;
Supporting facilities:Mansions,hotels,malls,banks,hospitals and other public utilities;
Refrigeration facilities:Chained supermarket and cold stores;
Chemical factories:Cooling system on production lines;
Manufacturers of electronic parts and components,semiconductor integrated circuits and liquid crystal displays,etc;
Specification parameters of condenser tube cleaning system
1. Performance index: Ball collection rate ≥99%
2. Input voltage:380V/50HZ (provide customization as required)
3. Power: ≤4KW
4. Requirements for working environment: Temperature ≤55ºC, relative humidity ≤95ºC
5. Pressure loss: 0.003MPa-0.05MPa
6. Applicable water temperature: ≤50ºC
7. Working pressure: ≤1.6MPa (customization for 2.5Mpa)
How to choose the type of condenser tube cleaning system
1.The design and selection of condenser tube cleaning system is determined by the refrigerating capacity of the chillers and the outlet pipe diameter of the cooling water.The size of balls shall be decided by the inner diameter of condenser heat transfer tubes of cold water host.
2.In order to prevent welding slags,welding rods,metal debris,sand and organic fabrics in the installation process,and the filling of cooling tower,corrosion in the cooling tubes and other foreign materials in the operation process from entering the condenser and evaporator,a less than 1.5mm precision of filter shall be installed in front of water inlet of chiller condenser (evaporator) and the effective filtering area of filter screen shall be 3 times larger than section area of the connecting pipe,to ensure proper water resistance of the filter.
Model code for condenser tube cleaning system
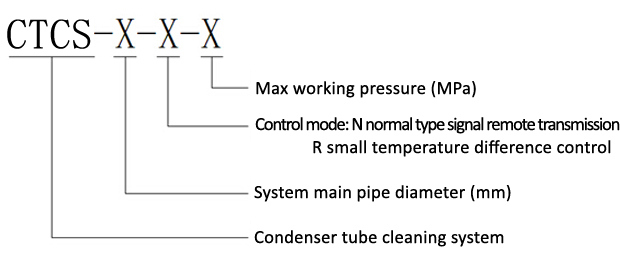
Specifications and models of condenser tube cleaning system
No. | Model | Selection guide, subject to actual cooling water pipe diameter |
1 | CTBC-150-N-1.6 | General host under 200 RT |
2 | CTBC-200-N-1.6 | General host between 200-500 RT |
3 | CTBC-250-N-1.6 | General host between 300-500 RT |
4 | CTBC-300-N-1.6 | General host between 500-800 RT |
5 | Irrigation Water Meter Bulk Water Meter,Woltman Water Meter,Cheap Woltman Water Meter Zhongfang Valve Xichuan Manufacturing Co., Ltd. , http://www.twt-zj.com |